В ноябре бетоносмеситель с самозагрузкой Fiori DB X35 был арендован для строительства общежития на Шубаркольском угольном разрезе.
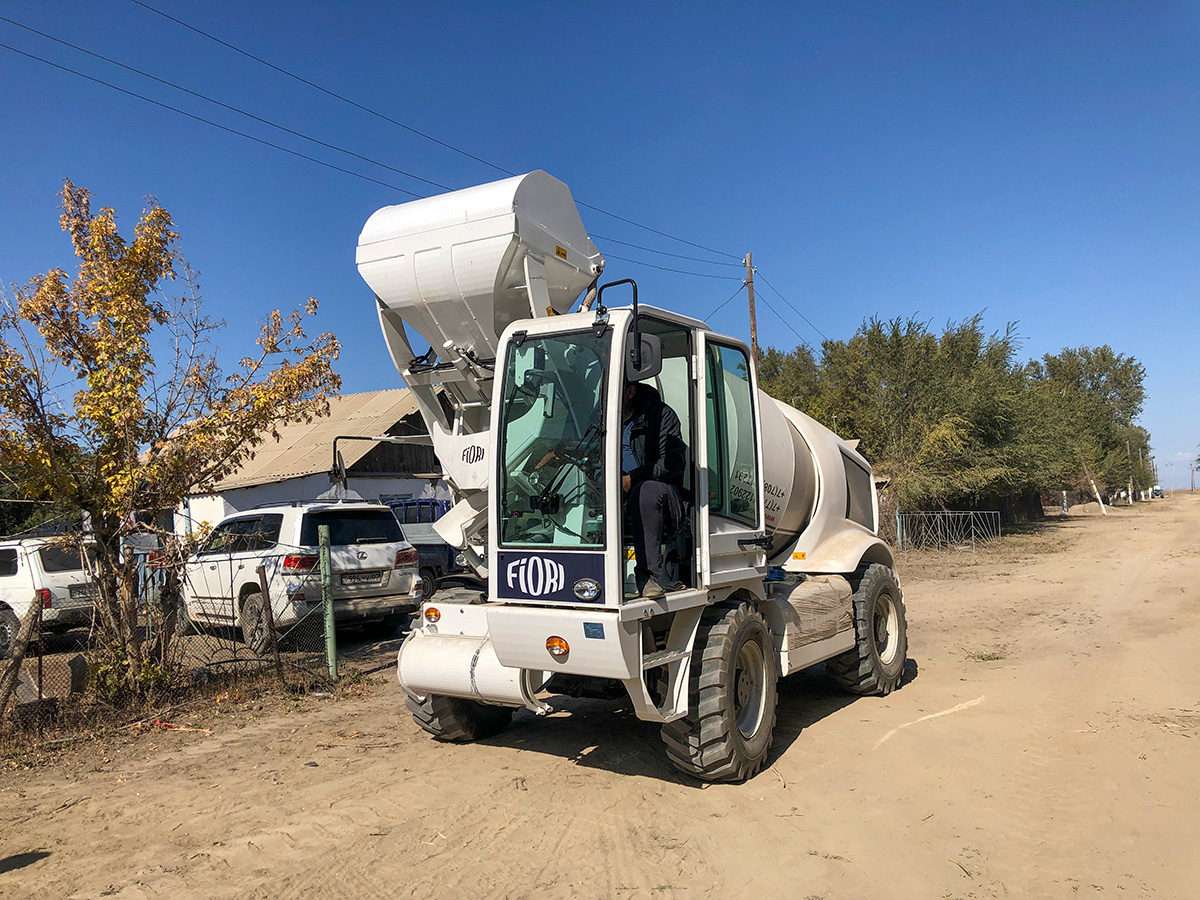
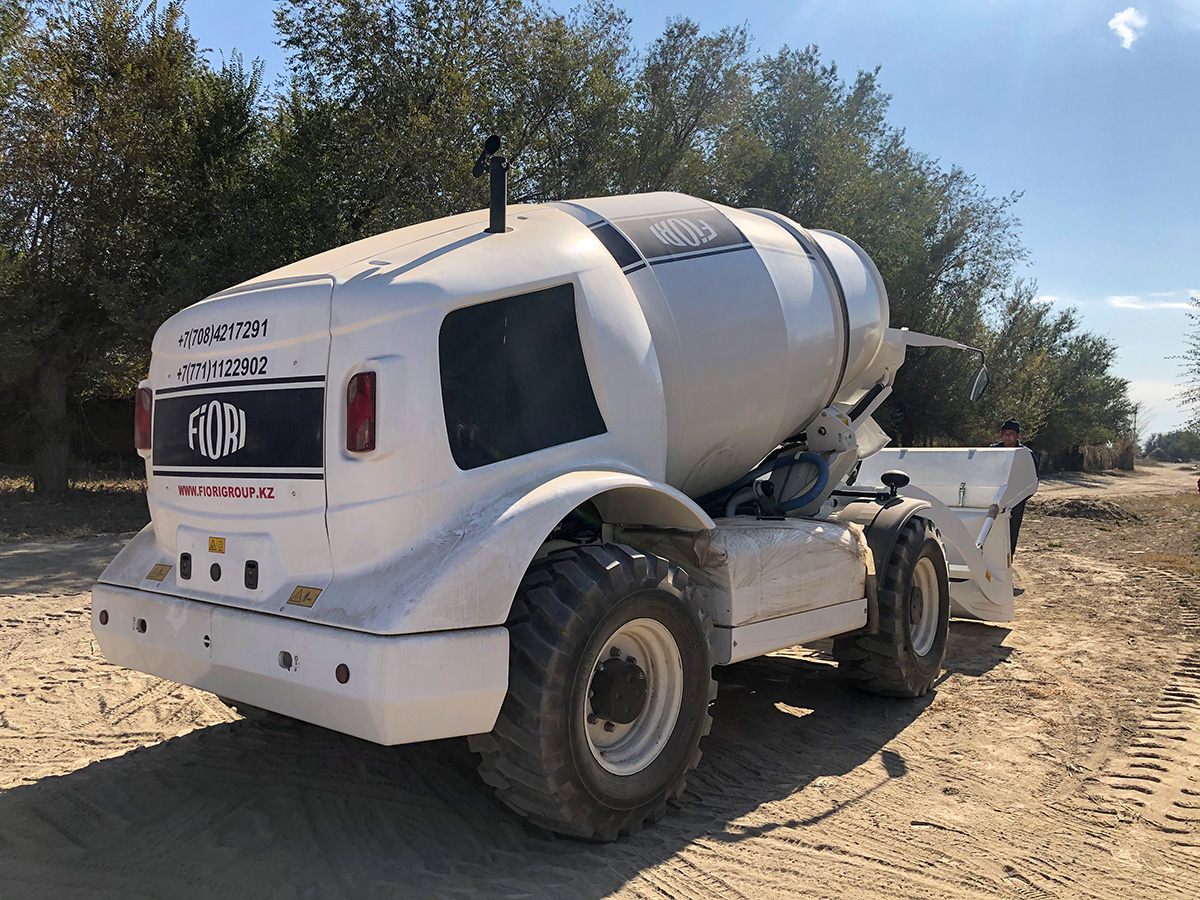
Обеспечить любое горное предприятие строительными материалами, в том числе и бетоном, задача не из простых. Все месторождения находятся в сотнях километров от крупных городов и, обычно, строят рабочие и вахтовые поселки для сотрудников.
Конечно же, с такими городками не будет рядом бетонного завода, с которого бы доставлялась смесь для строительства. Для горнорудных месторождений строительные материалы нужны не на постоянной основе и только в случае возведения новых объектов на предприятии или инфраструктуры вахтового поселка.
Расстояние от ближайших крупных населенных пунктов Шубаркольского месторождения слишком большое:
Нур-Султан – 357 км
Караганды – 465 км
Жезказган – 261 км
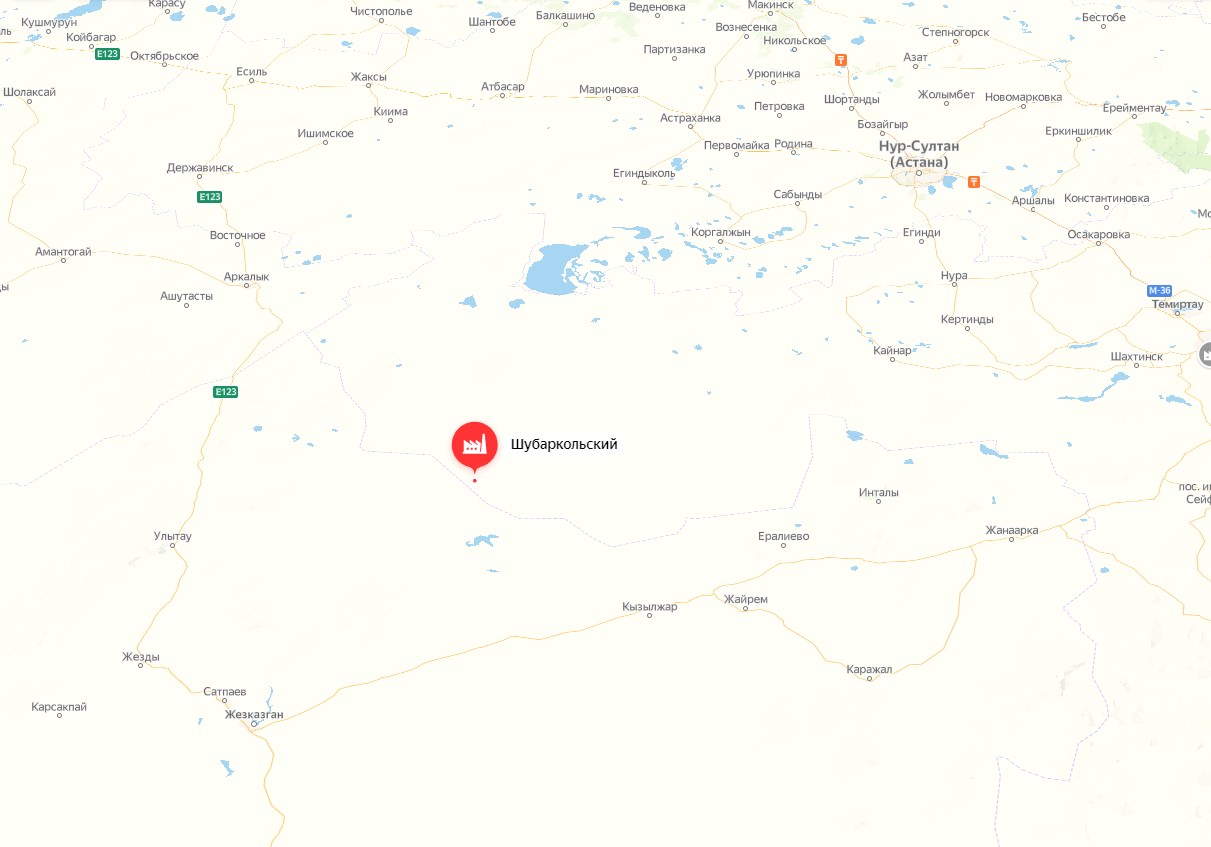
Бетонные заводы рядом с этими городами не возьмуться доставлять товарный бетон на подобные расстояния, так как дорога займет в лучшем случае более трех часов, и смесь невозможно будет использовать для строительства. Даже при замешивании пластифицирующих добавок бетон не выдержит длительной перевозки, начнется процесс схватывания и застывания еще в пути.
Тогда как обеспечить бетоном объект, который находится слишком далеко от бетонных заводов?
Таким же вопросом задался и наш клиент, “Шубарколь комир” – компания-производитель энергетического угля в Казахстане.
На угольном месторождении необходимо было построить трехэтажное общежитие. Но устанавливать стационарный бетонный завод только для одного объекта и потенциальных последующих построек – нецелесообразно. Доставка оборудования, установка, обслуживание и найм сотрудников для его функционирования затрачивает как временной, так и денежный ресурсы.
Как уже говорилось, постоянный процесс строительства не ведется на месторождении. Угольный разрез был открыт в 1983 году, и необходимая инфраструктура возводилась все это время.
Поэтому клиентом было принято решение арендовать Fiori DB X35.
Бетоносмесители с самозагрузкой Fiori – эффективный и производительный способ обеспечения бетоном стройплощадок, которые находятся в труднодоступной местности. Бетонная смесь производится прямо на объекте, поэтому ее качество не снизится из-за длительности доставки.
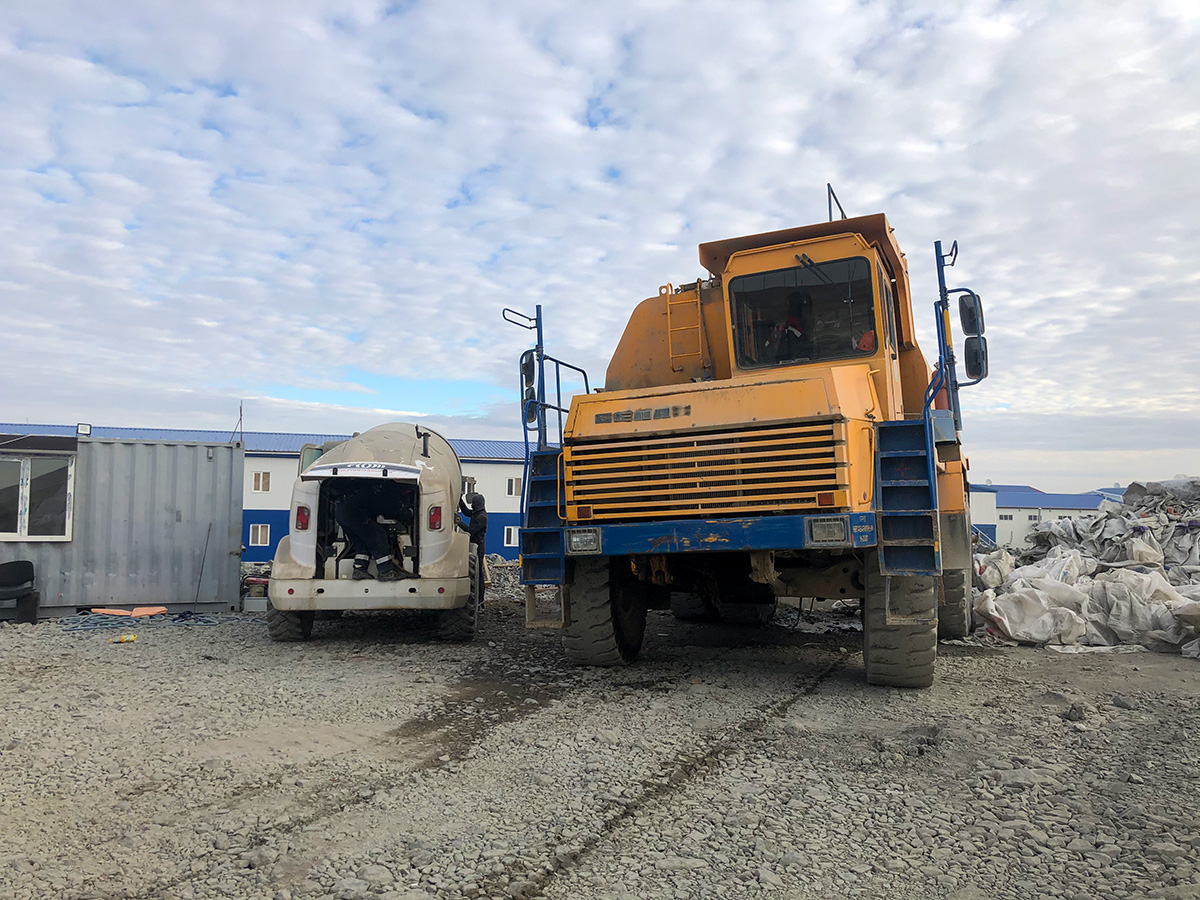
Многофункциональная и компактная спецтехника не требует сборки, установки, а готова сразу производить бетон, как только будет доставлен на объект. Для работы Fiori необходим только один оператор, который может управлять всем процессом загрузки материалов, замешивания, передвижения и выгрузки не выходя из кабины.
Полный цикл строительства общежития началось в конце ноября и продолжалось более полугода.
Забетонировать было необходимо конструкцию одного трехэтажного здания и инфраструктуру вокруг него: подъездную дорогу, тротуары.
Для того, чтобы бетоносмеситель мог показать весь свой максимум производительности, необходимо проверить условия, с которыми спецтехника будет работать:
– достаточный объем компонентов раствора
В труднодоступных местностях особенно важно иметь в наличии стройматериалы, так как подвоз материалов на объект может занимать не несколько дней, а недель или даже месяцев. В случае угольного месторождения были случаи, когда Fiori мог простаивать неделю из-за нехватки компонентов бетона.
– расположение материалов на стройплощадке
Если они находятся далеко друг от друга, то бетоносмеситель будет каждый раз тратить время на передвижение между ними и проезд до места выгрузки. При непрерывном производстве бетона это складывается в целые часы, в которые можно было произвести еще несколько десятков кубометров бетона.
Для строительства общежития все инертные находились близко к участку бетонирования и недалеко друг от друга. Поэтому Fiori тратил на загрузку инертных около 25 минут.
15 минут уходило на заполнение баков водой, которая бралась из подведенной к будущему зданию водопроводной системы. Остальные 10 минут уходили на другие компоненты. Щебень и песок загружались с помощью ковша. А цемент был упакован в бигбэги весом одну тонну. Мешки разрезали, поднимали с помощью крана и засыпали в ковш.
– подготовленность участка бетонирования
Чтобы спецтехника не простаивала, лучше заранее подготовить опалубку и объект к бетонированию. Fiori может быстро и непрерывно изготавливать бетон. Но, к сожалению, смесь невозможно просто выгрузить в резервуар и хранить, пока она не понадобится.
Наиболее частая ситуация, что бетоносмеситель длительное время ожидает, потому что площадка для выгрузки еще не армирована или рабочие только устанавливают опалубку.
На угольном месторождении спецтехнике также приходилось останавливать производство бетона, чтобы рабочие могли смонтировать опалубку. Но это не сказывалось критично на простое спецтехнике, так как занимали подобные простои не более половины дня, а после обеда Fiori уже покрывал всю дневную задачу по объему бетона.
Все три условия сильно влияют на длительность всего бетонирования и простой самоходного бетоносмесителя.
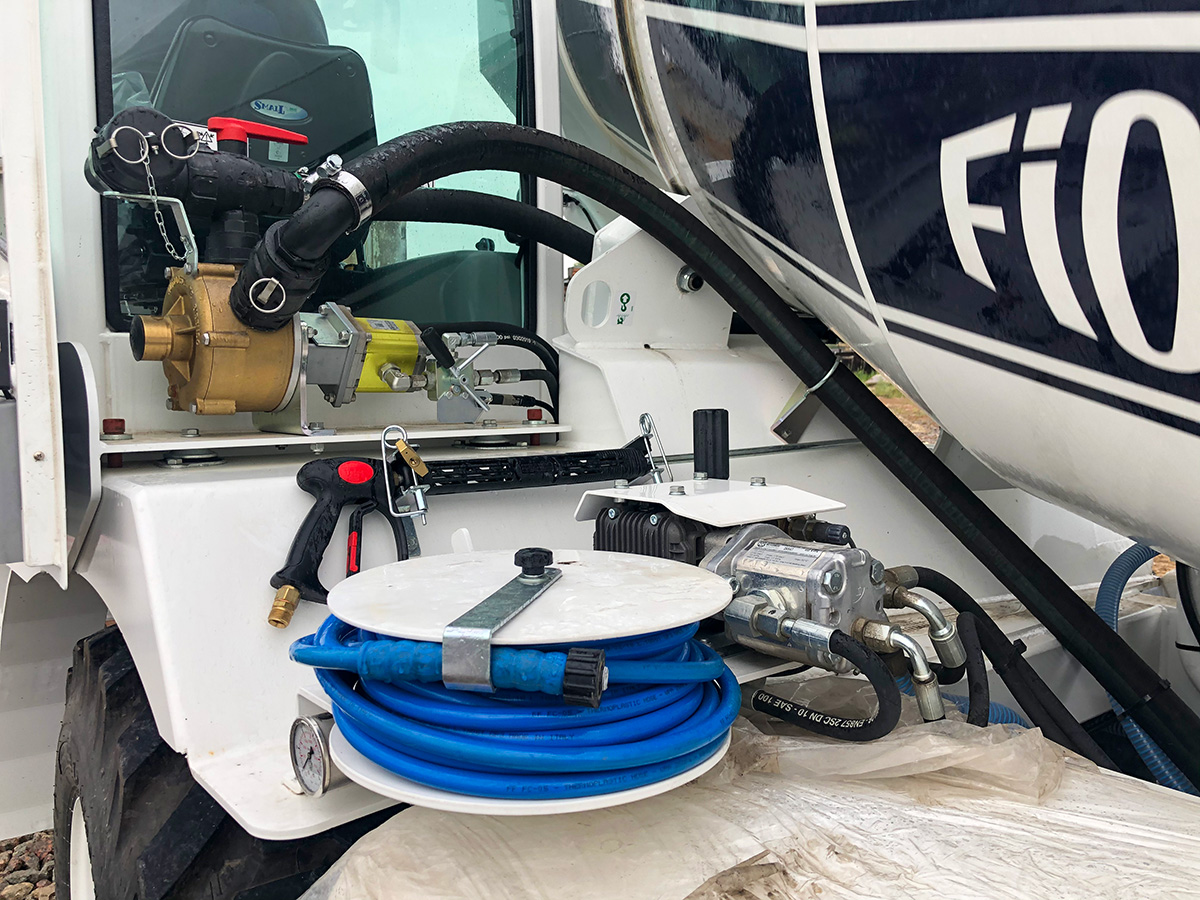
Почти все части конструкции, кроме фундамента, тротуаров и подъездных дорог бетонировали с помощью крана. Бетоносмеситель выгружал смесь в однокубовый конус, что иногда задерживало выгрузку. Fiori производил меньший объем за смену, чем мог бы. Спецтехнике приходилось ожидать, пока кран зальет смесь, чтобы снова выгрузить в него оставшуюся часть бетона.
Выгрузка вместе с изготовлением занимала от 40 минут до 2 часов, а замешанный раствор делили от 3 до 5 частей при заливке конусом. Время зависело от слаженности и длительности работы крановщика и рабочих, которые делали растяжку. А объем, который мог поднять конус, – от высоты выгрузки, потому что кран мог не выдержать полного объема конуса при бетонировании 2 и 3 этажей.
Когда Fiori доставили на объект, то сразу приступили к работе и за первые 10 дней произвел около 90м³ бетона для фундамента. За день спецтехнике удавалось сделать в среднем 3-4 замешивания.
Производительность модели DB X35 в идеальных условиях за час достигает до 4 циклов замешивания и до 14м³ бетона, а за смену – до 120м³.
На данном объекте был ряд причин, которые препятствовали бетоносмесителю производить его максимально возможный объем бетонной смеси, перечисленные выше. Но одна из причин задержек в производстве указана не была, так как повлиять на нее, увы, никто еще не в силах – погодные условия.
Климат в Казахстане характеризуется резкими перепадами температур. Зима продолжительная и холодная(до -50°С), лето – засушливое и жаркое (до 42°С). Подобные амплитуды сильно сокращают период, в который можно бетонировать конструкции, так и строительный сезон в целом.
Уже в начале строительства бетон производился при низких температурах воздуха, из-за чего каждое замешивание бетона задерживалось почти на всех этапах. При загрузке инертных два рабочих вскапывали и разбивали обледеневший песок и щебень. Если в материалах образовывались окаменелые комки, то рабочие выкидывали их.
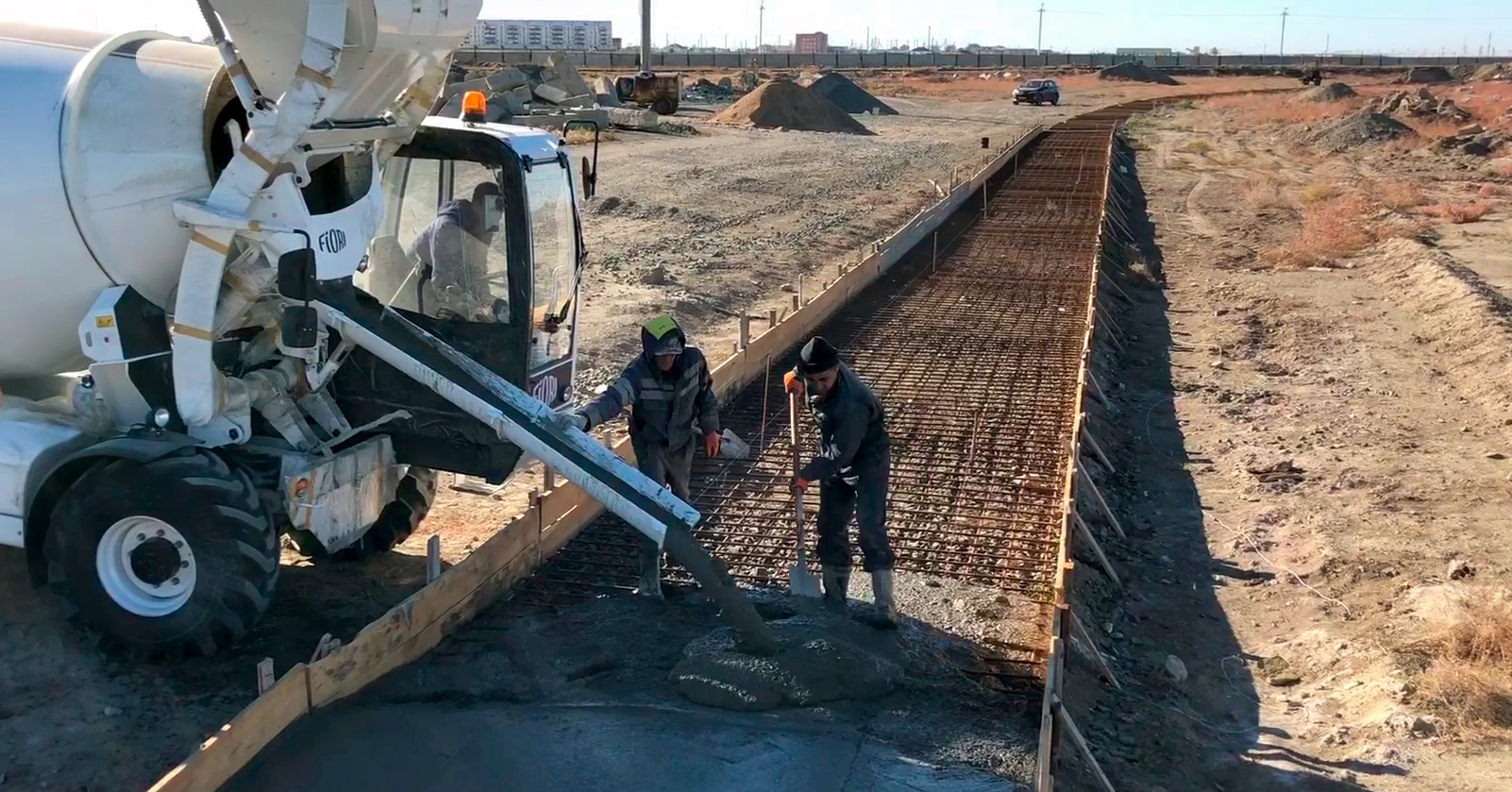
Но в смесительный барабан все еще могли попасть крупные камни, поэтому на конус, куда выгружалась бетонная смесь, надевали решетчатое сито и рабочие пристально наблюдали, и при попадании крупных окаменелостей рабочие выбрасывали их с решетки лопатами.
Смесь при заливке должна иметь определенную температуру, чтобы компенсировать смерзшиеся инертные и холодную погоду снаружи. Поэтому вместо обычной воды в баки загружалась вода из теплопровода.
На ночь спецтехнику ставили в теплый бокс, чтобы рабочие жидкости и сама техника не вымерзла.
Забетонированные объекты необходимо было утеплить, чтобы процесс схватывания конструкции не нарушился слишком низкими температурами. Все залитые бетоном участки накрывали тентами и ставили тепловые пушки на электрогенераторах.
Когда температура начала опускаться до -15 градусов, технический надзор запрещал проводить любые строительные процессы и приостановил строительство до улучшения погодных условий. Как раз за период, пока бетон не производился, на объект поставляли компоненты смеси и сендвич-панели, необходимые непосредственно в процессе бетонирования общежития, чтобы сократить время простоя спецтехники в дальнейшем.
При малейшем повышении температуры до допустимой, Fiori сразу начинал бесперебойно производить смесь. Пока все материалы для строительства основного здания не подвезли полностью, бетоносмеситель забетонировал всю инфраструктуру вокруг общежития – подъездные дороги, тротуары.
Когда погода улучшилась, выросла и производительность Fiori. За смену замешивалось до 40 кубометров раствора. При этом строительство все равно приходилось останавливать даже в теплое время года по усмотрению технадзора. Сильные порывы ветра свыше 10 м/с создавали опасные ситуации, когда объект бетонировали с помощью крана.
Все этапы строительства общежития начались с ноября и закончилось в июне. За время своих рабочих смен Fiori произвел и помог уложить около 500 кубометров бетона. Бетоносмеситель справился со своей задачей и выполнил ее в максимально возможные сроки даже в непростых условиях строительства:
- когда производство бетона происходило при минусовых температурах,
- большую часть времени использовалось дополнительное оборудование для выгрузки намного меньшим объемом, чем выход бетона за цикл у Fiori.